车床是最为常用的数控机床之一,主要用于轴类、套类等回转体零件的加工。计算机教程网将介绍关于数控车床加工入门的基础知识以及数控车床的加工工艺。
数控车床入门
数控车床是一种高度自动化的机床,它是用数字化的信息来实现自动化控制的,将与加工零件有关的信息--工件与刀具相对运动轨迹的尺寸参数、切削加工的工艺参数以及各种辅助操作等加工信息用规定的文字、数字和符号组成的代码,按一定的格式编写成加工程序单,将加工程序通过控制介质输入到数控装置中,由数控装置进行分析处理后,发出各种与加工程序相对应的信号和指令控制机床进行自动加工。计算机教程网首先介绍数控车床的分类与组成、数控车床的主要结构,对数控车床有一个入门性的了解。
数控车床的分类与组成
数控车床的类型
水平床身(卧式车床)。它有单轴卧式和双轴卧式之分。
单轴卧式车床由于刀架拖板运动很少需要手摇操作,所以刀架一般安放于轴心线后部,其主要运动范围也在轴心线后半部,使操作者易接近工件。采用短床身占地小,宜于加工盘类零件。双轴卧式车床便于加工零件的正反面。
倾斜式床身。它在水平导轨床身上布置三角形截面的床鞍。其布局兼有水平床身造价低和横滑板导轨倾斜便于排眉、易接近操作的优点。它有小规格、
中规格和大规格三种。
立式数控车床。它分单柱立式和双柱立式数控车床,采用立轴布置方式,适用于加工中等尺寸盘类和壳体类零件。便于装卸工件。
高精度数控车床。它分中、小规格两种,适用于加工精密仪器、航天及电子行业的精密零件。
四坐标数控车床。四坐标数控车床设有两个X、Z坐标或多坐标复式刀架可提高加工效率,扩大工艺能力。
车削加工中心。车削中心可在一台车床上完成多道工序的加工,从而缩短了加工周期,提高了机床的生产效率和加工精度。若配上机械手、刀库、料台
和自动测量监控装置构成车加工单元,用于中小批量的柔性加工。
各种专用数控车床。专用数控车床有数控卡盘车床、数控管子车床等
数控车床的基本组成
数控车床的整体结构组成基本与普通车床相同,同样具有床身、主轴、刀架及拖板和尾架等基本部件,但数控柜、操作面板和显示监控器却是数控机床特有的部件。即使对于机械部件,数控车床和普通车床也具有很大的区别。如数控车床的主轴箱内部省掉了机械式的齿轮变速部件,因而结构非常简单:车螺纹也不再需要另配丝杠和变换齿轮了:刻度盘式的手摇移动调节机构也已被脉冲触发计数装置所取代。下面以 CK7815 型数控车床和 CK9330型数控车床为例,简单介绍一下数控车床的结构组成。
CK7815 型数控车床是长城机床厂的产品,可选配 FANUC-6T 或FANUC-5T系统,为两坐标联动半闭环控制的CNC车床。该车床能车削直线(圆柱面)、斜线(锥面)、圆弧(成形面)、米制和寸制螺纹(圆柱螺纹、锥螺纹及多头螺纹),能对盘形零件进行钻、扩、铰和镗孔加工。
CK7815 型数控车床如图 1-1 所示。其床身导轨为 60°倾斜布置,排屑方便。导轨截面为矩形,刚性很好。主轴由直流(配 FANUC-5T 系统时)或交流(配
FANUC-6T 系统时)调速电动机驱动,主轴尾端带有夹紧液压缸,可用于快速自动装夹工件。床鞍溜板上装有横向进给驱动装置和转塔刀架,刀盘可选配 8位、12 位小刀盘和 12 位大刀盘。纵、横向进给系统采用直流伺服电动机带动滚珠丝杠,使刀架移动。尾架套简采用液压驱动。可采用光电读带机和手工键盘程序输入方式,带有 CRT 显示器、数控操作面板和机械操作面板。另外,还有液动式防护门罩和排屑装置。若再配置上、下料的工业机器人,就可以形成一个柔性制造单元(FMC)。
CK9330 型数控车床配有由华中数控研制开发的HCNC-1T 数控系统,是直接由计算机通过数控软件进行加工控制的新型 CNC 系统。该机床是一开环控制
的台式车床,其机械部分由床身、床头箱、工作台、大小拖板、普通刀架、尾架主轴电动机和 XZ 轴步进电动机(4NM、1NM 各一个)等组成,控制部分由机床强电控制柜、机械操作面板、计算机和数控软件等组成。CK9330 型数控车床的组成如图 1-2 所示。
数控车床的传动及速度控制
图 1-3 所示是 CK7815 型数控车床的传动系统图。主轴由 AC-6 型 5.5kW 交流调速电动机或 DC-8 型 1.1kW 直流调速电动机驱动,靠电气系统实现无级变速。
由于电动机调速范围的限制,故采用两级宝塔传动带轮实施高、低两档速度的手工切换,在其中某档的范围内可由程序代码 S 任意指定主轴转速。结合数控装置
还可进行恒线速度切削。但最高转速受卡盘和卡盘液压缸极限转速的制约,一般不超过 4500r/min。
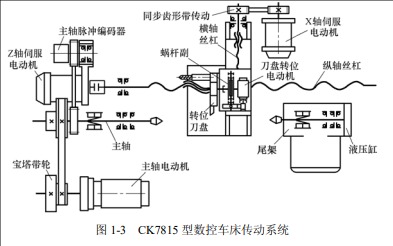
纵向 Z 轴进给由直流伺服电动机直接带动滚珠丝杠实现;横向 X 轴进给由直流伺服电动机驱动;通过同步齿形带带动横向滚珠丝杠实现,这样可减小横轴方向的尺寸。
刀盘转位由电动机经过齿轮及蜗杆副实现,可手动或自动换刀。排屑机构由电动机、减速器和链轮传动实现。
工进速度和快进速度还受控制面板上相应的速度修调旋钮影响。实际速度还应乘以速度修调的倍率。
CK9330 型数控车床的传动系统较为简单,该机床主轴是由电动机经三角胶带传至车头主轴,由传动带塔轮传动实施有级变速。主轴转速不受 S 代码的控制,其调整需靠手工进行。按图 1-3 所示变换各传动带位置,即可得到表 1-1 中所列的 6 级主轴转速。由于主轴转速不可无级调控,所以在车削螺纹时,只有靠编码器检测主轴的实际转速并反馈到数控系统后,再由系统自动调整进给轴的进给速度来保证(主轴每转一圈,刀架移动一个螺距值)。
CK9330 型数控车床的纵向 Z 轴进给由 4N·m 的三相六拍感应式步进电动机直接带动普通丝杠实现,横向 X 轴进给由 1N·m 的步进电动机带动一对 18/27的减速齿轮后,再带动普通丝杠实现。由于小拖板上的丝杠手柄调节位移量不计入数控装置,因此只用于加工前对刀时的辅助调节,它在加工过程中的任何移动都将影响尺寸精度。
CK9330 型数控车床的主要规格与技术参数如表 1-1 所示。
CK9330 型数控车床的主要规格与技术参数
床身上最大工件回转直径
|
300mm
|
加工米制螺纹螺距
|
0.5~3mm(或更大)
|
最大工件长度
|
500mm
|
加工寸制螺纹种数
|
20
|
刀架上最大工件回转直径
|
140mm
|
加工寸制螺纹螺距
|
11~40 牙/in
|
主轴通孔直径
|
26mm
|
纵、横向进给量级数
|
无级调速
|
主轴孔莫氏锥度
|
NO.4
|
主轴每转刀架的纵、横向进给量
|
无级调速
|
刀架最大横向行程
|
160mm
|
主轴转速范围
|
160~1600r/min
|
刀架最大纵向行程
|
100mm
|
主轴转速级数
|
6
|
加工米制螺纹种数
|
14
|
|
|
此外,还有些车床的主轴虽然采用的是机械式的有级变速,但配合一定的电液动控制系统,也可通过 S 代码自动实现主轴的变速,但只能是有级变速。
数控车床的控制面板及其功能
用计算机作控制系统的数控车床,其程序输入、数据设定和 NC 控制等操作均可用计算机的键盘进行,文字和图形信息由显示器显示。CK9330 型数控车床操作面板的布局如图 1-4 所示。
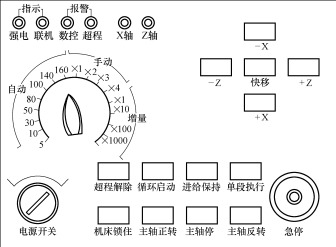
1-4 CK9330 型数控车床的操作面板
面板顶行为一排指示灯,分别为指示机床电柜电源的“强电”指示灯、表示机床与计算机数控软件是否联系上的“联机”指示灯、数控系统内部是否有故障的“数控”报警和控制轴行程是否超界的“超程”报警指示灯,以及回参考点指示灯。右上部按菱形布置的几个按钮为拖板移动用的手动操作按钮,相当于传统车床上的旋转手柄,轴移动方向遵循标准规定。当按住某轴移动方向按钮的同时再按住中间的快移按钮时,则该轴将以内部设定的最快速度向指定方向移动;否则,将以当前设定的速度修调率移动。指示灯下方的旋钮为速度修调旋钮,“自动”的各档用于控制机床自动及 MDI 方式下的进给速度修调率,“手动”各档用于控制点动及步进移动时的 X、Z 轴移动速度,“增量”各档则用于决定步进方式下点按一下轴移动按钮所产生的移动量。左下方的 NC 锁匙电源是为机床提供的又一道电源开关。右下方的急停按钮用于紧急情况下强行切断电源。中部为以下几个功能控制按钮:
1)超程解除。当 Z 轴正负方向出现硬性行程超界时,可同时按此按钮和 Z轴相反方向的按钮以解除超程。
2)循环启动、进给保持。用于自动运行中暂停进给和持续加工。
3)单段执行。在自动运行方式下,若按下此钮,则每执行一段程序后都将暂停等待,需按循环启动方可执行下一段程序。
4)机床锁住。若按下此按钮,则程序执行时只是数控系统内部进行控制运算,可模拟加工校验程序,但机械部件被锁住而不会产生实际的移动。
5)主轴正转、反转和停。用于手动控制主轴的正转、反转和停转。
控制软件的环境界面如图 1-5 所示,图中屏幕顶行为状态行,用于显示工作方式及运行状态等,工作方式按主菜单变化,运行状态在不同的工作方式下有不同的显示。
(1)自动运行时显示
1)5%~140%(自动运行的进给速度修调倍率)。
2)循环停止(自动运行处于暂停状态)。
3)机床锁住(机械锁住有效时)。
4)程序单段(单段运行有效时)等。
(2)MDI 方式时显示
1)当前默认的 G 代码模态值(如 G00 G91 G21 G94)。
2)点动操作方式:5%~100%(最大速度百分比)。
3)X 轴进给或 Z 轴进给。
4)步进功能方式:×1、×10、×100、×1 000(四种步进倍率)。
5)X 轴进给或 Z 轴进给。
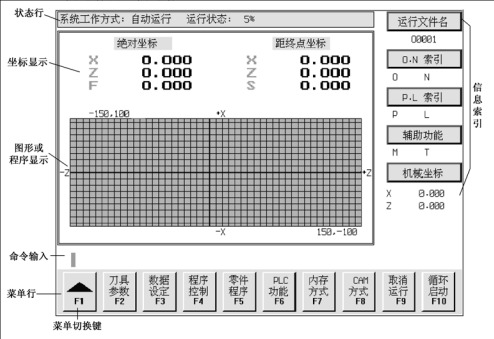
1-5 控制软件的环境界面
屏幕中间为工件加工的坐标显示和图形跟踪显示或加工程序内容显示。
屏幕下部为提示输入行和菜单区(多级菜单变化都在同一行中进行)。
屏幕右部为信息索引显示区:“O.N 索引”处显示自动运行中的 O 代码(主程序号)和 N 代码(程序段号);“P.L 索引”处显示自动运行中的 P 代码(子程序调用)和 L 代码(调用次数);“辅助功能”处显示自动运行中的 M 代码(辅助功能)和 T 代码(刀具号和刀补号);“机械坐标”处显示刀具在机床坐标系中的坐标变化。
控制软件系统的整个菜单显示切换均在屏幕底行上进行,菜单选取由功能键F1~F10 操作。第一级子菜单的调出和所有下级菜单的往上退回均靠 F1 功能键实施。例如:在主菜单级显示时,按下 F2 键选中自动运行方式后,该按钮呈凹下状,但需要再按 F1 键方可切换到自动运行方式的下级菜单。然后,在本级菜单显示时,按下相应的选用功能键,即可自动调用显示下级菜单或执行相应的菜单项功能(即除第一级子菜单调出需按 F1 键外,往下层次的子菜单调出,则不需按 F1 键,均可自动调出)。若从本级菜单返回到上一级菜单,以及当本级某菜单项执行完后又想执行本级的另一菜单项功能时,则需要按 F1 功能键,而不是按Esc 键;若在主菜单显示时按了 Esc 键,则自动退出控制软件系统。
数控车床控制系统的功能
数控机床上数控系统的硬件有各种不同的组成和配置,再安装不同的监控软件,就可以应用于不同机床或设备的控制,这样数控系统就有不同的功能。具体如下:
(1)多坐标控制功能 控制系统可以控制坐标轴的数目,指的是数控系统最多可以控制多少个坐标轴,其中包括平动轴和回转轴。基本平动坐标轴是 X、Y、Z 轴;基本回转坐标轴是 A、B、C 轴。联动轴数是指数控系统按照加工的要求可以控制同时运动的坐标轴的数目。如某型号的数控机床具有 X、C、Z 三个坐标轴运动方向,而数控系统只能同时控制两个坐标(XZ、XC 或 ZC)方向的运动,则该机床的控制轴数为三轴(称为三轴控制),而联动轴数为两轴(称为两联动)。
(2)插补功能 插补功能指数控机床能够实现的运动轨迹,如直线、圆弧、螺旋线、抛物线、正弦曲线等。数控机床的插补功能越强,说明能够加工的轮廓种类越多。控制数控车床的系统一般只有直线和圆弧两种插补功能。
(3)进给功能 进给功能包括快速进给、切削进给、手动连续进给、自动加减速等功能。进给功能与伺服驱动系统的性能有很大的关系。
(4)主轴功能 主轴功能可实现恒转速、恒线速度、定向停止等功能。恒线速度指的是主轴可以自动变速,使得刀具对工件切削点的线速度保持不变。主轴定向停止功能主要用于数控机床在换刀、精镗等工序退刀前对主轴进行准确定位,以便于退刀。
(5)刀具功能 刀具功能指在数控机床上可以实现刀具的自动选择和自动换刀。
(6)刀具补偿功能 刀具补偿功能包括刀具位置补偿和半径补偿功能。半径补偿中包括对车刀的刀尖半径和刀尖朝向的补偿。
(7)机械误差补偿功能 机械误差补偿功能指系统可以自动补偿机械传动部件因间隙产生的误差的功能。
(8)操作功能 数控机床通常有单程序段运行、跳段执行、连续运行、试运行、机械锁住、进给保持和急停等功能,有的还有键盘操作功能。
(9)程序管理功能 程序管理功能指对加工程序的检索、编制、修改、插入、删除、更名和锁住。
(10)图形显示功能 在显示器(CRT)上进行二维或三维、单色或彩色的图形显示。图形可进行缩放、旋转,还可以进行刀具轨迹动态显示。
(11)辅助编程功能 辅助编程功能如固定循环、图形缩放、子程序、宏程序、坐标系旋转和极坐标编程等功能,可减少手工编程的工作量和难度。
(12)自诊断功能 自诊断功能指数控系统对其软件、硬件故障的自我诊断。这项功能可以监视整个机床和整个加工过程是否正常,并在发生异常时及时报警。
(13)通信与通信协议 现代数控系统一般都配有 RS232C 接口或 DNC 接口,可以与上级计算机进行信号的高速传输。高档数控系统还可与工厂自动化局域网
(MAP)或Internet相连,以适应柔性制造系统(FMS)、计算机集成制造系统(CIMS)的要求。
以上是一般可用于机床的数控系统的基本功能。对于用于数控车床的数控系统还有其自身的特点。首先,数控车床所需要控制的坐标轴的数目比较少。一般的数控车床只需要控制两个坐标轴(X 轴和 Z 轴);对于高等级数控车床(或者数控车削中心),一般也只需要控制三个或四个坐标轴(X、Z、C、Y 轴);只是对于某些特殊类型的数控车床(如双主轴或双刀架的车削中心),对控制坐标轴的数目的要求才比较高。其次,数控车床对可以联动的坐标轴的数目要求也比较少,一般为两轴联动或三轴联动。这样与数控铣床或加工中心相比,数控车床对数控系统的要求就相对低一些。至于对数控系统其他功能的要求,与其他机床没有太大的区别,只是要求具备恒线速度(恒表面速度)的功能,这是由车削加工的特点决定的。
数控车床的主要结构特点
数控车床因其加工方法和特点,配合不同类型的车削刀具,主要应用于具有复杂回转型面工件的自动加工和各类螺纹的加工。目前已广泛应用于民用产品和军工产品的加工生产中,是应用最为广泛的数控机床之一。与传统车床相比,数控车床的结构有以下特点:
1)由于数控车床刀架的两个方向运动分别由两台伺服电动机驱动,所以它的传动链短,不必使用变换齿轮、丝杠等传动部件,用伺服电动机直接与丝杠连接带动刀架运动。伺服电动机丝杠间也可以用同步传动带副或齿轮副连接。
2)多功能数控车床是采用直流或交流主轴控制单元来驱动主轴的,按控制指令做无级变速,主轴之间不必用多级齿轮副来进行变速。为扩大变速范围,现在一般还要通过一级齿轮副,以实现分段无级调速,即使这样,主轴箱内的结构已比传统车床简单得多。数控车床的另一个结构特点是刚度大,这是为了与控制系统的高精度控制相匹配,以便适应高精度的加工。
3)数控车床的第三个结构特点是轻拖动。刀架移动一般采用滚珠丝杠副。滚珠丝杠副是数控车床的关键机械部件之一,滚珠丝杠两端安装的滚动轴承是专用轴承,它的压力角比常用的向心推力球轴承要大得多。这种专用轴承配对安装,最好在轴承出厂时就是成对的。
4)为了拖动轻便,数控车床的润滑都比较充分,大部分采用油雾自动润滑。
5)由于数控机床的价格较高、控制系统的寿命较长,所以数控车床的滑动导轨也要求耐磨性好。数控车床一般采用镶钢导轨,这样机床精度保持的时间比较长,其使用寿命也可延长许多。
6)数控车床还具有加工冷却充分、防护较严密等特点。自动运转时,一般都处于全封闭或半封闭状态。
7)数控车床一般还配有自动排屑装置。
数控车床的技术参数
数控车床的主要技术参数包括最大回转直径、最大车削长度、各坐标轴行程、主轴转速范围、切削进给速度范围、定位精度、刀架定位精度等,其主要技术参数如表 1-2 所示。
表 1-2 数控车床的主要技术参数
类 别
|
主 要 内 容
|
作 用
|
尺寸参数
|
X、Z 轴最大行程
|
影响加工工件的尺寸范围(质量)、编程范围及
刀具、工件、机床之间干涉
|
卡盘尺寸
|
|
最大回转直径
|
|
尾架套筒移动距离
|
|
最大车削长度
|
|
接口参数
|
刀位数、刀具装夹尺寸
|
影响工件及刀具安装
|
主轴头形式
|
|
主轴孔及尾架孔锥度、直径
|
|
运动参数
|
主轴转速范围
|
影响加工性能及编程参数
|
刀架快进速度、切削进给速度范围
|
|
动力参数
|
主轴电动机功率
|
影响切削载荷
|
伺服电动机额定转矩
|
|
精度参数
|
定位精度、重复定位精度
|
影响加工精度及其一致性
|
刀架定位精度、重复定位精度
|
|
其他参数
|
外形尺寸(长×宽×高)、质量
|
影响使用环境
|